
OK, I hope you can still remember part-one of the story about aramid fibers that I wrote last week, if not, click here to review.
Today, I want to go a bit deeper into the story of aramid fibers.
It is quite possible that you have not heard of aramid fibers before reading our last blog. However, the chances are that many if not most of you have heard of carbon fiber, or you will have seen something made out of "carbon fiber". Why do I add the quotation mark to carbon fiber? Because the truth is that a lot of what you see is just as much about aramid fiber as it is carbon fiber.
To give you some examples, both aramid fiber and carbon fiber can be used as a key material in body armor, but it is quite hard to tell one from the other just by looking at their appearance. Similarly, there are a lot of carbon fiber phone cases on the market today, which happen to look very similar to aramid fiber phone cases. Due to the misleading information given out by some manufacturers, a lot of users as well as retailers have mistaken one for the other. But, they are in fact they are two completely different products.
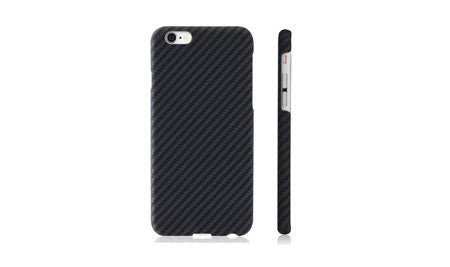
Aramid iPhone 7 Case
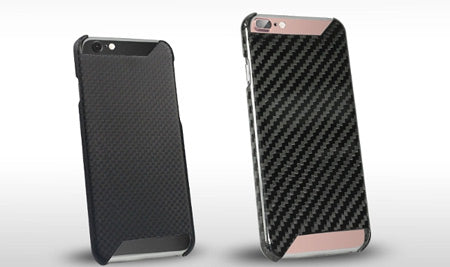
Carbon Fiber iPhone 7 Case
As both of these materials are being used more and more widely, it's very likely that you will come across these products. So, how about learning some more about aramid fiber and carbon fiber? You will then be able to make a more educated decision when you need to buy something or you might even wow your friends and colleagues with your amazing knowledge.
1. The Colors
#Aramid Fiber
Aramid fiber, in its natural state, is a bright golden yellow color. However, in recent years, scientists have been able to develop distinct colors such as black, red, orange, green or blue.
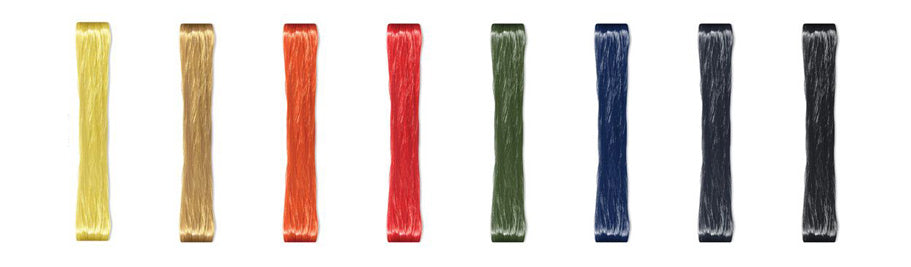
DuPontTM Kevlar® Yarn Color Samples
#Carbon Fiber
Carbon fiber, on the other hand is always black and will always be black, it cannot be colored. The only way to change carbon fiber's appearance is by blending it with something, with what you might ask? Well, some coloured aramid fiber of course.
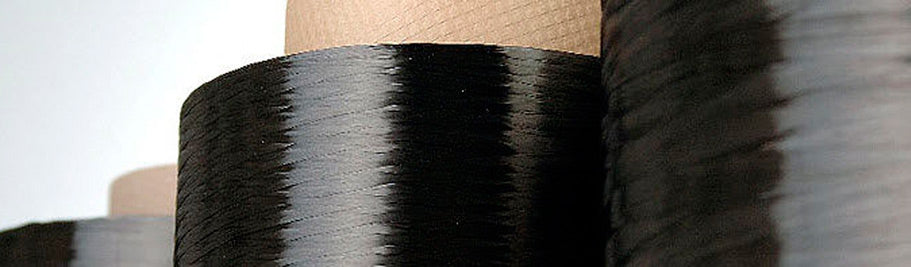
Carbon Fiber Yarn Natural Color
2. The Weave
#Aramid Fiber
When woven together, aramid cloth comes in two types of weaves, the plain one and the twill one. Twill weave is typically used where improved flexibility is required, whilst the plain weave is very common in composites because it offers uniform properties, maximum stability as well as simple surfacing characteristics.
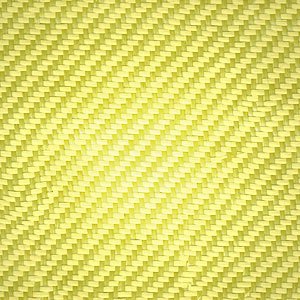
Twill Weave
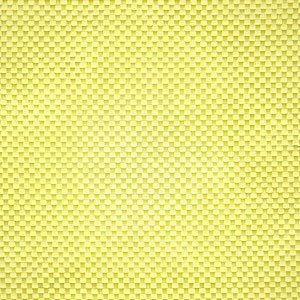
Plain Weave
#Carbon Fiber Weave
Classic carbon fiber fabrics are woven toward their fiber orientation and are commonly used in the composites industry and as per the aramid fiber, they include plain and twill weaves. The plain weave is less pliable and more cut-resistant, whilst the twill weave has fibers that run straighter and longer, maintaining the theoretical strengths of the fiber as well as making it more pliable and stronger than the plain weave.
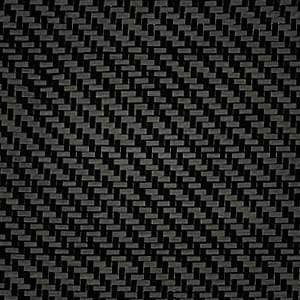
Twill Weave
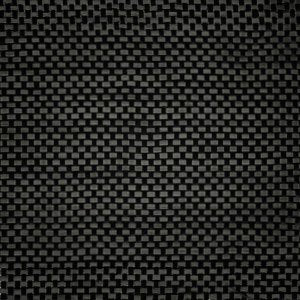
Plain Weave
#Carbon-Aramid Hybrid Fabrics
As well as the classic weaves of these two types of fiber, aramid can be woven into Hybrid Fabrics which are blended with carbon fiber. This way the properties of the combined fibers are enhanced by synergy. (Synergy is the creation of a whole that is greater than the simple sum of its parts)
Or, to put it in another way, when combining two or more fibers, the resulting material tends to keep the stronger properties whilst giving up the weaker ones. Thus, a hybrid weave fabric is often the preferred choice for many composite manufacturers.
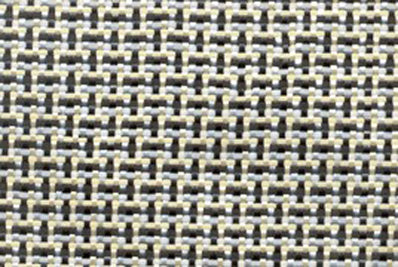
Carbon-aramid-polyester-glass Hybrid Fabric
3. The Costs
If you check the price of both materials, you will find that they are comparable over a given length, but the final price can depend on other factors as well. Additionally, aramid fiber and carbon fiber are more expensive when compared to other composite materials such as fiberglass. You can see more in terms of price differences by looking at reputable online sites such as Fibreglast.
One additional aspect to understand is that as emerging technologies become more main stream, those best-in-class carbon fiber costs start to come down each year, as you can see in the following table.
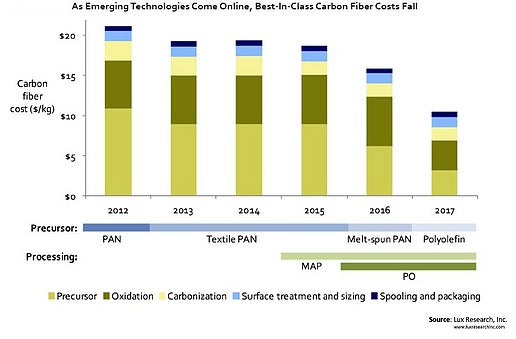
4. The Properties
A: Density
Density (or volumetric mass density) refers to a substance's mass per unit volume.
Therefore, the denser a material is, the heavier it will feel for an equal volume.
When you compare the density of Aramid fiber to carbon fiber, you will find that they are different. If you were to hold two equal sized blocks of carbon fiber and aramid fiber in your hands, you would be able to tell which is which without opening your eyes as Kevlar is lighter.
Diameter | Specific Gravity | Density of Laminate grams/cc |
|
---|---|---|---|
Carbon Fiber | 5-10 | 1.8 | 1.58 |
Kevlar 29 | 12 | 1.45 | 1.43 |
Kevlar 49 | 12 | 1.45 | 1.45 |
Kevlar 129 | 1.5 | 1.44 | |
Kevlar 149 | 1.45 | 1.45 |
(Note: The figures given here involve only carbon fiber and aramid fiber. For more information, please have a look at our last blog for the data on some other relevant materials)
B: Strength-to-weight ratio
The strength-to-weight ratio is a material's force per unit area at failure divided by its density.
Kevlar has a high strength-to-weight ratio when tested unidirectionally (as in the direction of the fibers). Both Kevlar and carbon fiber have very good strength-to-weight ratios.
Fiber Strength | Laminate Strength | Strength-to-weight Ratio KN.m/kg. |
|
---|---|---|---|
Carbon Fiber | 4127 | 1600 | 2457 |
Kevlar | 2757 | 1430 | 2514 |
C: Tensile Strength
Tensile strength is the maximum stress a material can hold, when being pulling apart before it breaks down.
Some non-brittle materials distort before breaking, but Kevlar and carbon fiber are brittle and therefore they will break without distortion. The measurement of Tensile strength is stated as the force per unit area, Pa or Pascals. Tensile strength can also refer to the ultimate tensile strength or ultimate strength.
Ultimate Tensile Strength MPa |
|
---|---|
Carbon Fiber | 2757 |
Kevlar 29 | 4137 |
Kevlar 49 | 3450 |
Kevlar 129 | 1600 |
Kevlar 149 | 1500 |
D: Modulus of elasticity
Young's Modulus is a measure of the stiffness of a solid material.
A mechanical property of linear elastic solid materials, it defines the relationship between stress and strain (Young's Modulus is the ratio of stress to strain).
Young's Modulus = Stress/ Strain
In other words, a material with a high Young's Modulus is stiffer than a material with lower Young's Modulus.
Young's Modulus GPa |
|
---|---|
Carbon Fiber | 125-181 |
Aramid Fiber | 70.5-186 |
E: Electrical Conductivity
Carbon fiber has great electrical conductivity, I think that this is well known. Your chemistry teacher must have explained that to you in middle school.
In contrast however, aramid fiber, as I mentioned last week, is a great insulator, and its dielectric strength is up to 20kv/mm.
The problem is, if you forget that carbon fiber is a great conductor, it could be a real problem for you. For example, perhaps you fancy a smart carbon fiber case (which seemed to be getting quite popular) for your phone; this would be great to look at, but terrible for your phone's cell signal.
But why?
Well, by transmitting and receiving electromagnetic waves your phone gets it's a signal and joins the cellular phone network. Unfortunately, carbon fiber's conductive properties will significantly absorb, reflect and counteract these electromagnetic waves. So, the signal of your phone with a carbon fiber case will decrease dramatically.
This is very similar to other conductive phone cases such as metal ones. Carbon fiber cases have been known to reduce signal strength by anything from 40% to 60% on average. Ironically, both carbon fiber and metal cases are very popular amongst the general public due to their style and sleek design.
Oh and if you insist on using a carbon fiber case, do take it off if you would like it to survive outside on rainy days.
Those people in the know will choose the aramid fiber phone case instead of carbon fiber, because whilst they look very similar and stylish, the aramid fiber case will NOT reduce your signal strength at all. Perfect!
F: Others
Carbon Fiber | Aramid Fiber | |
---|---|---|
Resistance to Abrasion | Good | Better |
Resistance to Solvents | Good | Better |
Melting Point | High | No Melting Point |
Flammability | High | Low |
5. The Production Process
#Aramid Fiber Manufacturing
As mentioned in last blog, aramid fibers actually include two types, para-aramid and meta-aramid and the manufacturing methods are different for each one.
Meta-aramid is made from the polymer poly-metaphenylene isophthalamide, whereas the para-aramid is manufactured from polymer p-phenylene terephthalamide.
Aramid fibers are produced from these polymers by using either the wet or the dry spinning method; this is because the aramids would decompose before they melted. A polymer solvent, anhydrous sulphuric acid is used to help with the spinning processes.
In wet spinning, a strong solution of the polymer and inorganic salts is used. This is spun and extruded through a spinneret into a weak acid or water bath, which removes the salts and leaves the yarn.
In the dry spinning process, the salts are harder to remove, so this process is typically only used to produce the meta-aramid fibers.
In both processes, post treatment of the fibers is handled by additional drawing, which optimizes the fiber's properties.
#Carbon Fiber manufacturing
The production of carbon fiber is based on PAN-based (polyacrylonitrile-based) or pitch-based precursors.
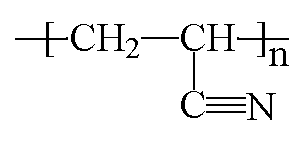
PAN (polyacrylonitrile) Monomer
The precursors go through a number of different operations during the production.
Stage one, involves passing them through very high temperatures to oxidize the precursors. Stage two, involves the precursor being treated with chemicals to give high stiffness-to-weight and strength-to-weight properties to the pre-material. After a surface treatment and sizing stage, the materials resin compatibility and handle properties have also been greatly improved.
Depending upon the precursor used to make the fiber, carbon fiber may be turbostratic or graphitic, or even a hybrid structure with both graphitic and turbostratic parts present. Carbon fiber derived from PAN are turbostratic, while carbon fiber produced from pitch are graphitic after heat treatment at temperature exceeding 2200℃. The weight of PAN during oxidation and carbonization is reduced by 50% of its original weight.
The production of carbon fiber is mainly based on PAN-based fibers (a polymeric fiber material with a textile basis) whilst Pitch fiber is achieved by spinning purified petroleum or coal-tar pitch, the resulting fibers have a high degree of molecular orientation which gives a higher moduli and improves thermal conductivity.
The production process of carbon fiber is very slow and expensive because of the time and energy consuming processes involved. Pitch-based carbon fibers and PAN-based fibers are produced in similar ways. But pitch is more difficult to spin and the resulting fiber is more difficult to handle.
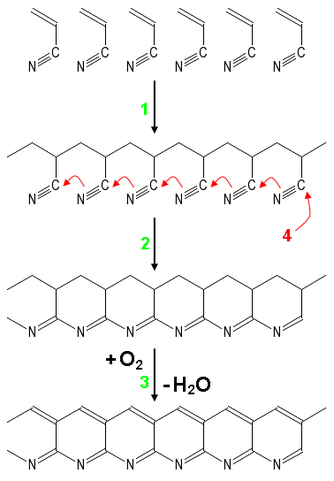
Synthesis of Carbon Fiber from PAN
6. Aramid Fiber VS. Carbon Fiber: Who is the Winner
So, after going through our comprehensive analysis. Hopefully, you will be a little clearer in the differences between these two very interesting fibers.
But what exactly does that mean to those manufacturers who use these materials?
Well, that depends on what they are trying to do with it.
In short, if the strength of the material is the only consideration, then the stronger aramid fiber is the better choice. However, if it's the stiffness that you need, then you go for carbon fiber.
Oh and if you are going to buy a stylish phone case, remember, there is no point in choosing a carbon fiber case because it will ruin your signal strength.
Instead, the right choice is to go for a phone case made from Aramid Fiber, the perfect replacement for a carbon fiber case.