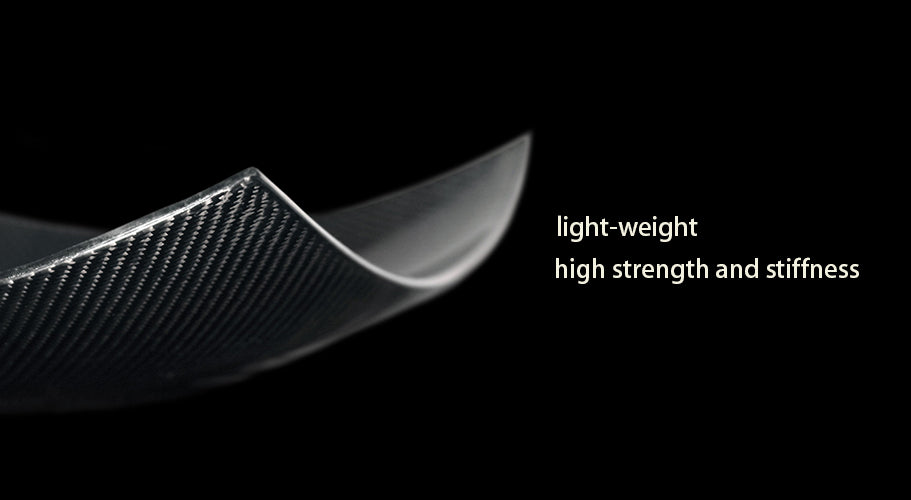
1. The Definition of Composite Material
A composite material is made by combining two or more natural or artificial materials with the resultant material having better properties than the two materials alone. There are two constituent parts to a composite material, the reinforcements and the matrix.
The new material is usually noted for being stronger, lighter, and less expensive than traditional materials. They differ from other materials in the world, sometimes their usage is not obvious and it can be discovered by accident or sheer luck.
However, a composite material is usually developed with a particular application in mind and this will often require a long development and testing process to ensure that it does what it is supposed to do. Their usage is becoming more and more widespread, from the building trade to automobile industry, from the marine industry to the aerospace industry.
Composite materials are widely used in:
- Concrete, the most common artificial composite material
- Reinforced plastics, for example the fiber-reinforced polymer (FRP)
- Metal Matrix composite (MMC)
- Ceramic Matrix composite (CMC)
2. The Constituents
There are several phases involved in composite production.
The reinforcing phase provides the rigidity and stiffness. In most cases, the reinforcement is harder, stronger and tougher than the matrix.
- Reinforcements
The reinforcement is usually a fiber or a particulate. Particulate composites tend to be weaker and more flexible than fiber composites, in part, due to the processing difficulties. They are typically more brittle in nature as they usually contain less reinforcement.
Reinforcements can be divided into two types, continuous fiber-reinforced materials and discontinuous (short) fiber-reinforced materials, as shown below. The continuous fiber-reinforced material will often have a layered or laminated structure (a), while the discontinuous (short) fiber-reinforced material will have a random orientation, appearing as chopped fibers or matting (b).
Typical reinforcement types
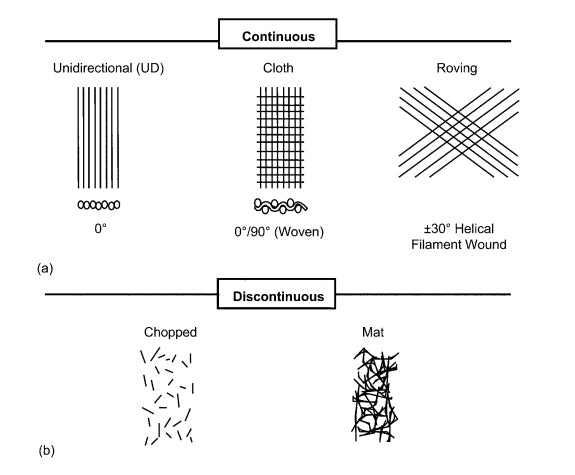
The most common fibers include glass fibers, aramid fibers and carbon fibers, all of which can be either continuous or discontinuous.
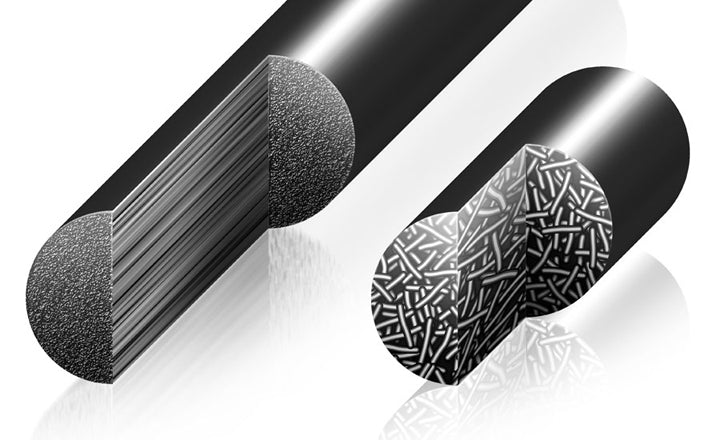
Long-Short Carbon-Fiber-Reinforcement Comparison
Reinforcement generally adds strength and stiffness to composite materials and this greatly reduces the chance of cracking. It is not just the thick fiber reinforcement that helps, even thin fibers are likely to have high strength and if they are mechanically well attached well to the matrix, they are able to improve the properties of the composite dramatically.
- Matrix
The continuous phase is also known as the matrix, which is normally a polymer, a metal, or a ceramic. Polymers have low strength and stiffness, metals have intermediate strength and stiffness but can have high ductility, whilst ceramics have high strength and stiffness but will also be more brittle.
The matrix can be divided into two types, organic and inorganic. Organic matrices such as Polymers are very common (especially for fiber reinforced plastics) and are typically used to create composites containing fiberglass, carbon fiber or aramid fiber. Whilst inorganic matrices are often employed in concrete, metals, ceramics and glasses.
The matrix plays some critical functions:
- Maintaining the fibers in the required orientation
- Reducing the chances of abrasion and compression
Polymer and Metal based matrix composites have a strong bond between the fiber and the matrix, which enables the load stresses to be transferred through to the fibers. In a Ceramic matrix composite, the matrix is primarily used to increase the toughness of the composite rather than the strength or stiffness.
Matrices are further classified as either a thermoplastic, a short fiber thermoplastic, a long fiber thermoplastic or a long fiber-reinforced thermoplastic. Many of the advanced thermoset polymer matrix systems usually incorporate aramid fibers and carbon fiber in an epoxy resin matrix.
Major polymer matrix composite fabrication processes
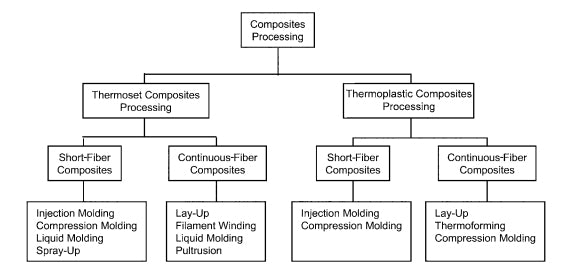
3. Application
- For Construction
As a construction material, concrete is the most commonly found artificial composite material and typically consists of loose stones with a matrix cement. It's a mixture of cement and aggregate, giving a robust, strong material that is very widely used throughout the world. In the United States alone, concrete production is a $30-billion-per-year industry and globally, the ready-mix concrete industry, the largest segment of the concrete market exceeded $100 billion in revenue in 2015.
Concrete is not expensive to manufacturer and it is strong in compression. However, concrete has a poor tensile strength, making it easy to break apart when stretched. To help reduce this, an additional material such as steel bars, certain plastic or ceramic bars are embedded within the concrete. These high tensile strength materials help the concrete to withstand greater loads when being tensioned.
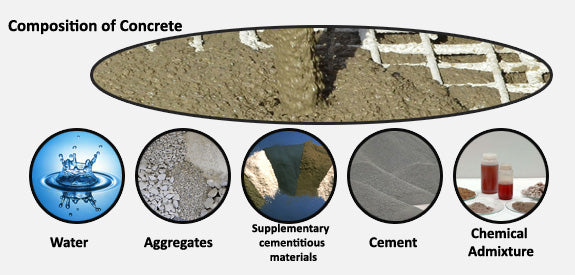
Compositions of concrete
- For Aircraft/ Military
In general, the high-performance but more costly-effective carbon-fiber composites or aramid-fiber composites are used where high stiffness and light weight are required. Whilst the much lower-cost fiberglass composites are used in less demanding applications where strength and weight is not as critical.
In military aircraft, low weight is the 'king' for performance and payload reasons. So currently, carbon-fiber composites and aramid-fiber composites are the best materials to use in manufacturing. The same is now happening within the commercial aircraft industry and perhaps, the most striking example of this goes to the new Boeing 787, where the primary material used in the manufacturing of the airframe is composite materials.

Materials of Boeing 787 Dreamliner Commercial Airplane. Source: Modern Airliner
As shown on above picture, among the 50% of advanced composites, the carbon laminate composite and carbon sandwich composite make up a large percentage.
- For Automobiles
The major automobile manufacturers are increasingly turning to composites to help them meet increasingly strict performances and weight targets, ultimately improving fuel efficiency and also cutting down on the manufacturing costs. The most typical materials being used are fiberglass/polyurethane and fiberglass/polyester.
As well as the above mentioned composite materials, some of the more high-end manufacturers have used carbon fiber to great effect. Tesla, Ferrari, Lamborghini and many other manufacturers have increased the use of carbon fiber to reduce weight, increase stiffness and strength, from the interior to small body parts through to entire chassis components.
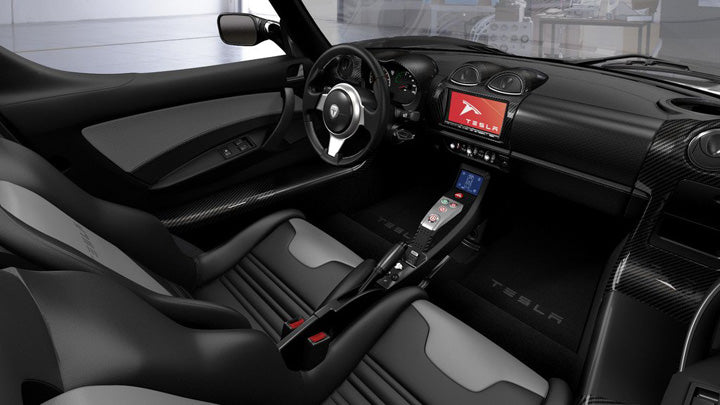
Tesla Interior Carbon Fiber Kit
By adopting carbon fiber for its interior design, door sills, upper door sills, instrument binnacle, stereo and centre console trim, Tesla has greatly enhanced the look and sportiness of the car with the added benefit of reducing the overall weight of the vehicle.
-The Other
Other Applications of Composite Materials
Applications | Examples |
---|---|
Appliance | Cooking appliances, dishwashers, refrigerators, laundry, ice machines and small appliances |
Energy | Wind turbines, fuel cells, solar panels and pumps |
Marine | Engine covers, personal watercraft, boat access covers, motor housing |
Sanitary / Plumbing | Faucets, sinks, drains, showers and bathtubs |
Jewelry | Phone cases, laptop cases, instrument cases, jewelry, watches etc |
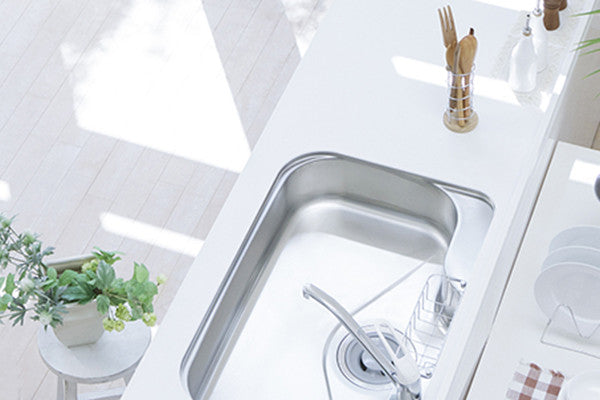
Sinks made of composite materials
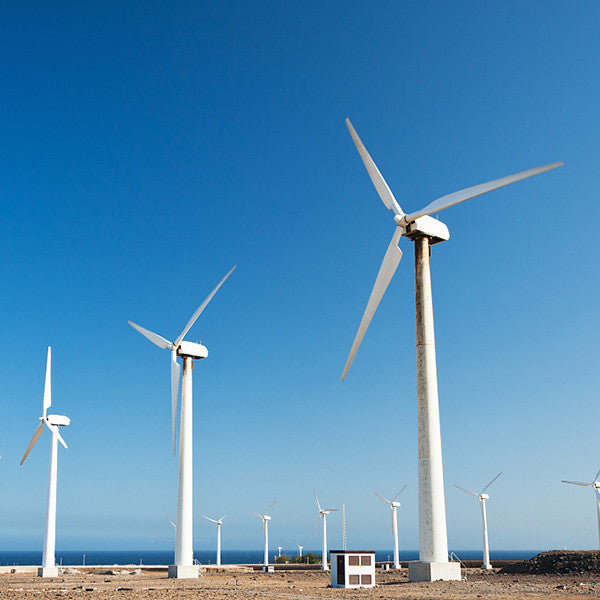
Wind turbines made of composite materials
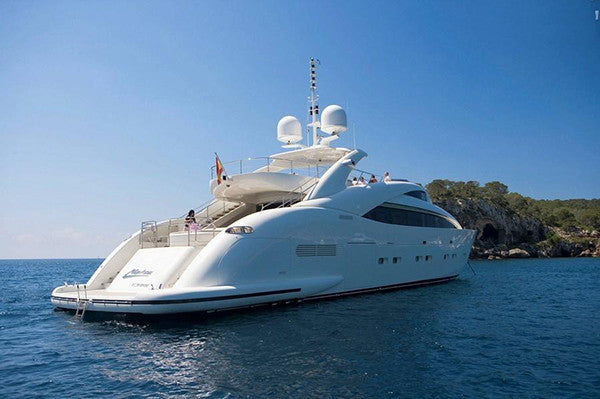
Marine composites
4. History Overview
Going back thousands of years, man started combining materials such as straw and mud, a crude form of composite which was used to improve the building of houses, whilst ancient brick making has been recorded in Egyptian tomb paintings. Since these early times, man's use of composites has grown throughout every walk of life to the vast array of applications that we have today.
The History of Composite Materials
Time | Development of Composite Material |
---|---|
Around 3400 B.C. | At around 3400 B.C., man glued wood stripes at different angles to create Plywood. |
2181-2055 B.C. | Egyptians use layers of linen or papyrus soaked in plaster to create cartonnage, dating back to 2181- 2055 B.C. |
Around 1500 B.C. | Ancients use straws to reinforce mud bricks, pottery, and boats. |
Around 1200 A.D. | The Mongols invented the first composite bows made of a combination of wood, bamboo, bone, cattle tendons, horns, bamboo and silk bonded with natural pine resin. |
1870s - 1890s | Polymerization allowed new synthetic resins to be transformed from a liquid to solid state in a cross-linked molecular structure. |
Early 1900s | Plastics like vinyl, polystyrene, phenolic and polyester were developed. |
1930s | Owens corning launched the fiber reinforce polymer (FRP) industry by introducing the first glass fiber. In 1936, unsaturated polyester resins were patented. |
1940s | WWII brought the FRP industry from research into actual production. By 1947, a fully composite body automobile had been made and tested. |
Early 1950s | Manufacturing methods such included pultrusion, vacuum bag molding, and large-scale filament winding were developed. Filament winding became the basis for the large-scale rocket motors that propelled exploration of space in the 1960s and beyond. |
1960s | In 1961, the first carbon fiber was patented, and carbon fiber composites were used commercially after several years. The marine market was the largest consumer of composite materials in the 1960s. |
1970s-1980s | In the 1970s, the automotive market surpassed marine as the biggest market for composite materials - a position it retains today. |
1990-2000 | By the mid-1990s, composites hit mainstream manufacturing and construction as a cost-effective replacement to traditional materials. Consumers came into contact with composite materials every day from handles to the beautifully stained entry doors at their homes. In the mid-2000s, the development of 787 Boeing Dreamliner validated composites for high-strength and rigid applications. |
Present Day | The development of composite materials is constantly increasing its application in automotive, appliances and consumer products industries. And now composites are just beginning to find their way into nanotechnology. According to the statistics from marketsandmarkets, the global market size of composite materials is projected to grow from USD 69.50 Billion in 2015 to USD 105.26 Billion by 2021, at a CAGR (Compound Annual Growth Rate) of 7.04% between 2016 and 2021. |
The Future | The research into composite materials is attracting more and more attention from governments, manufacturers and universities. This will drive more investments to help with the inventing of more fibers and resins. This will lead to more applications of composite materials in both existing and new industries. It is also extremely likely that environment-friendly composite materials like recycled plastics and bio-based polymers will increase in use. |
5. Why PITAKA Choose Composite Materials
As previously discussed, lightweight is an important feature, which explains why composite materials like aramid fiber and carbon fiber are being increasingly used in the automobile and aircraft industries. Likewise, for an 'Every Day Carry' (EDC) phone case or wallet, lightness is extremely important.
For the PITAKA Team, one of our design goals was to make products, which are strong, high quality and in no way detracting from the designs of the products that you want us to protect. This is why we use composite materials.
Moreover, the EDC accessories that PITAKA offer are designed with ultimate beauty and simplicity. Oh, and of course, ultimate durability, an essential characteristic in all our designs here at PITAKA.
And that's one of the things that composite materials do best, in part due to their outstanding properties, but also if you take a composite material like carbon fiber or aramid fiber in a plain weave or twill weave pattern, they demonstrate very minimalistic aesthetics on their own. Now, when we take them and apply them to our products, you get something truly special and unique.
Mr Yutaka (Designer of PITAKA) has always believed that every EDC is not only for carrying but also an extension of you. So we are always pursuing beautiful-looking, durable products and well, we are making them.
So, why not check out the range of PITAKA composite material products and allow them to speak for themselves! Step on PITAKA journey here.